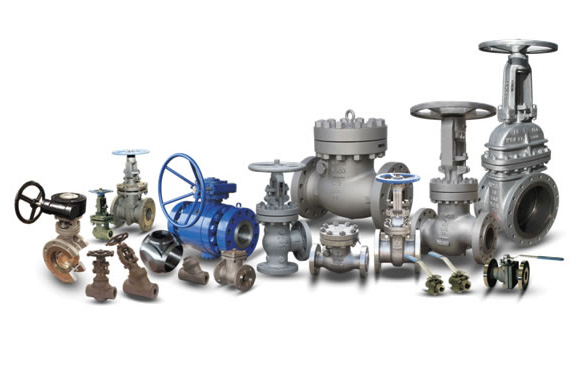
Learn about the different types of valves used in the oil and gas industry and their differences: API and ASME gate, globe, check, ball, and butterfly designs (manual or actuated, with forged and cast bodies). Briefly said, valves are mechanical devices used in piping applications to control, regulate and open/close the fluid’ s flow and pressure. Forged valves are used for small bore or high-pressure piping applications, cast valves for piping above 2 inches.
WHAT IS A VALVE?
The different types of valves used in the petrochemical industry suit any of the following applications:
1. Start/stop the flow of the fluid (hydrocarbons, oil & gas, steam, water, acids) through the pipeline (example: gate valve, ball valve, butterfly valve, knife gate valve, or plug valve)
2. Modulate the flow of the fluid through the pipeline (example: globe valve)
3. Control the flow of the fluid (control valve)
4. Change the direction of the flow (for example a 3-way ball valve)
5. Regulate the pressure of a process (pressure reducing valve)
6. Protect a piping system or a device (pump, motor, tank) from overpressures (safety or pressure relief) or back-pressures (check valve)
7. Filter debris flowing through a pipeline, to protect equipment that may be damaged by solid parts (y and basket strainers)
A valve is manufactured by assembling multiple mechanical parts, the key ones being the body (the outer shell), the trim (the combination of the replaceable wetted parts), the stem, the bonnet, and an actioning mechanism (manual lever, gear or actuator).
Valves with small bore sizes (generally 2 inches) or that require high resistance to pressure and temperature are manufactured with forged steel bodies; commercial valves above 2 inches in diameter feature cast body materials.
VALVE BY DESIGN
● GATE VALVE: This type is the most used in piping and pipeline applications. Gate valves are linear motion devices used open and close the flow of the fluid (shutoff valve). Gate valves cannot be used for throttling applications, i.e. to regulate the flow of the fluid (globe or ball valves should be used in this case). A gate valve is, therefore, either fully opened or closed (by manual wheels, gears or electric, pneumatic and hydraulic actuators)
● GLOBE VALVE: This type of valve is used to throttle (regulate) the fluid flow. Globe valves can also shut off the flow, but for this function, gate valves are preferred. A globe valve creates a pressure drop in the pipeline, as the fluid has to pass through a non-linear passageway.
● CHECK VALVE: this type of valve is used to avoid backflow in the piping system or the pipeline that could damage downstream apparatus as pumps, compressors, etc. When the fluid has enough pressure, it opens the valve; when it comes back (reverse flow) at a design pressure, it closes the valve – preventing unwanted flows.
● BALL VALVE: A Ball valve is a quarter-turn valve used for shut-off application. The valve opens and closes the flow of the fluid via a built-in ball, that rotates inside the valve body. Ball valves are industry standard for on-off applications and are lighter and more compact than gate valves, which serve similar purposes. The two main designs are floating and trunnion (side or top entry)
● BUTTERFLY VALVE: This is a versatile, cost-effective, valve to modulate or open/close the flow of the fluid. Butterfly valves are available in concentric or eccentric design (double/triple), have a compact shape and are becoming more and more competitive vs. ball valves, due to their simpler construction and cost.
● PINCH VALVE: This is a type of linear motion valve that can be used for throttling and shut-off application in piping applications that handle solid materials, slurries and dense fluids. A pinch valve features a pinch tube to regulate the flow.
● PLUG VALVE: Plug valve is classified as a quarter-turn valve for shut-off applications. The first plug valves were introduced by the Romans to control water pipelines.
● SAFETY VALVE: A safety valve is used to protect a piping arrangement from dangerous overpressures that may threaten human life or other assets. Essentially, a safety valve releases the pressure as a set-value is exceeded.
● CONTROL VALVE: these are valves to automate complex petrochemical processes.
● Y-STRAINERS: while not properly a valve, Y-strainers have the important function of filtering debris and protect downstream equipment that may be otherwise damaged
Post time: Oct-26-2019